公司新闻
COMPANY NEWS
服务新闻
COMPANY NEWS

生产排程无法提质增效?APS了解一下
前言:
精益生产和敏捷制造逐渐成为主流生产路线。
生产中各类排程难题:
1、客户订单预交期评估难、回复慢、算不准;
2、排产计划编制困难、耗时长工作强度大;
3、遗漏产能因素,排产计划准确度低;
4、实际生产变化大,排程计划难调整;
等等
排程难题解决有方
在制造企业与客户达成合作前,客户有时会对企业的交货期进行评估,以此为依据判断企业对订单是否具备“交期、品质、成本”三项满足能力。
接到订单后,随之而来的难题就是车间对“材料、人员、设备”三要素的分配、调派和使用。随着精益生产的流行和制造企业利润空间变薄,企业的关注重点开始向如何平衡各机器和工人的生产负荷,节约时间人力成本,摆脱瓶颈提高产能利用率等问题转移。
东信达APS系统以追求精益生产(JIT)为目标,能够为复杂的生产和供应问题提供优化解决方案,广泛适用于各类制造型企业。能均衡生产过程中各种生产资源,在不同的生产瓶颈阶段给出最优的生产排程计划,实现快速排程并对需求改变做出快速反应。
在智能制造大环境下,APS的作用被越来越多制造企业认识并做出有益尝试。下面将谈谈,东信达APS究竟如何赋能生产制造呢?
你无法绕开APS实现数字化转型
一位有多年车间管理经验的工作人员表示,“很多时候决策者更在乎怎么安排生产资源更能节约时间成本、提高产能利用率。但管理方式摆在这了,可优化空间真的很少。”
数据驱动让一切变得简单起来。在保证在订单交付水准提高的前提下,APS能帮助实现“高产能、低成本”的高精度优化运作。
同时随着继承和保留人员经验、生产数据的不断积累,它能遵循车间的实际运作模式,实现交付、产出和成本的持续优化,让生产“向数字化要效益”。这也是很多制造企业数字化转型的终极目标——管理赋能业务。
数据赋能决策
在车间产能需求和物料需求数据长期分析的过程中,也为产能拓展、供应链构建(找更好的供应商)等提供决策依据。
▲图表形式展示
主计划排程—计划下发生产任务
精益管理,灵活强大
▲东信达APS系统模块流程
让生产管理更透明
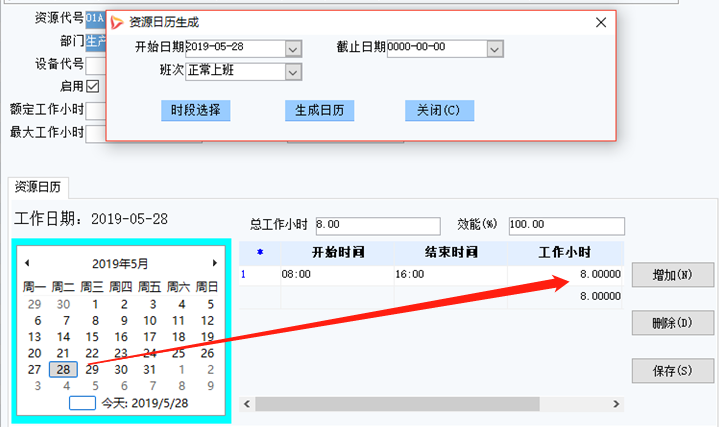
能够有效降低过去设备闲忙不均、人心不齐、订单交付日期不定等问题,使生产管理更透明化、直观化,管理层也能更好把控生产进度,及时揪出问题。
专业实施 更懂你的行业
一开始便对所有排程参数及规则设置了最为通用、合理的默认值。即使是新员工也能迅速上手操作,大大节约了APS系统融入企业管理框架的磨合时间。
随着企业对业务的扩展,用户也可以方便地对各项参数进行调整。让APS解决方案更贴合企业生产管理!智能工厂中,数据才是第一生产力。企业不再属于“肩抬人扛”的工业时代,谋求变革的第一要义便是认识到数据驱动的重要性。这样,才能逐渐向自动化、智慧化的智造工厂转型进步!