公司新闻
COMPANY NEWS
服务新闻
COMPANY NEWS

如何用看板系统快速提升生产效率?
前言
2019年的制造企业更加举步维艰。前有各项生产运营成本日益上涨的不可逆趋势,后有中美贸易摩擦的严重影响,内外夹击,使得企业更需要在逆境中求生存及发展。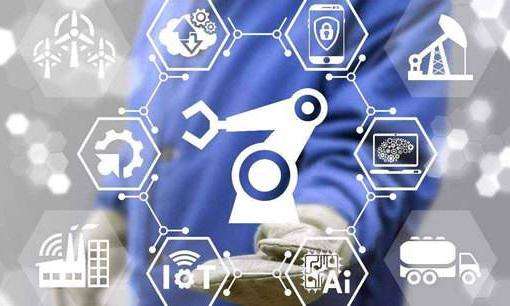
虽然智能制造、智慧车间等理念已经深入人心,但是如何结合企业实际情况,既能高瞻远瞩,又能灵活务实,稳健推进企业的智能制造水平,是摆在企业和信息化供应商的难题。
东信达MES核心:约束理论+看板系统
东信达公司一直致力于协助制造企业提升综合管理水平,尤其是智能制造水平。在针对生产效率和车间管理的解决方案上,有着20年如一日的执着,多年来已形成自己的专业产品体系和实施方法。坚持以约束理念为指导思想,以结果导向推动过程改善,以点带面的看板系统作为关键技术手段,是保证其众多项目能在短期内快速上线,成功率极高的重要秘诀。
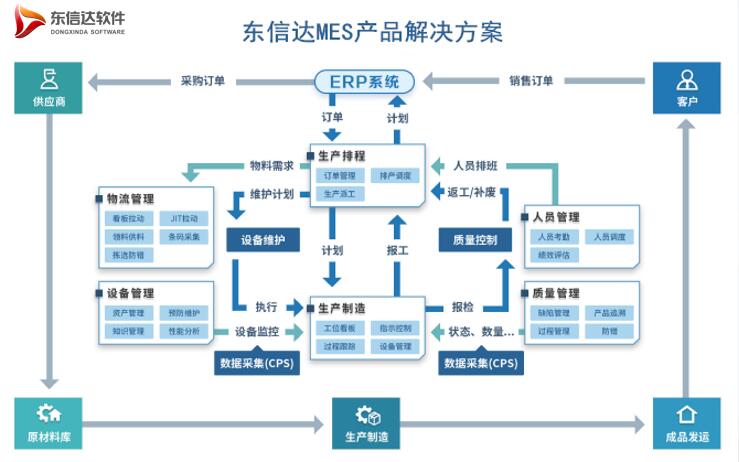
东信达可依据自身产品优势,结合不同企业的现场及管理实际难题,为不同的企业制定出相对简单、务实、高性价比的解决方案和信息技术,并帮助企业快速落地。
永龙项目成效及项目概况
项目成效
永龙车间信息化项目就是其中一个典型例子。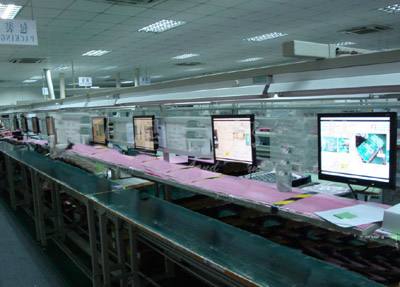
- 运行赘余时间的缩短使整个生产流程用时进一步缩短了10%。
- 提升了管理人员和操作人员的工作协调性,同时最大限度规避了失误。
- 装配后的头三个月,车间工人的考勤准确率提升了10%,同等工作量的完工时间提早了近15%,出错概率从之前的3%降低到不足1%。
项目分析
永龙汽车灯具有限公司是一个仅成立几年的年轻公司,专业生产汽车灯具,产品有频闪灯、警示灯、工作灯等四百多种,不但在国内市场受到诸多好评,更远销海外,在欧美、中东、东南亚等国有着稳定的供应链。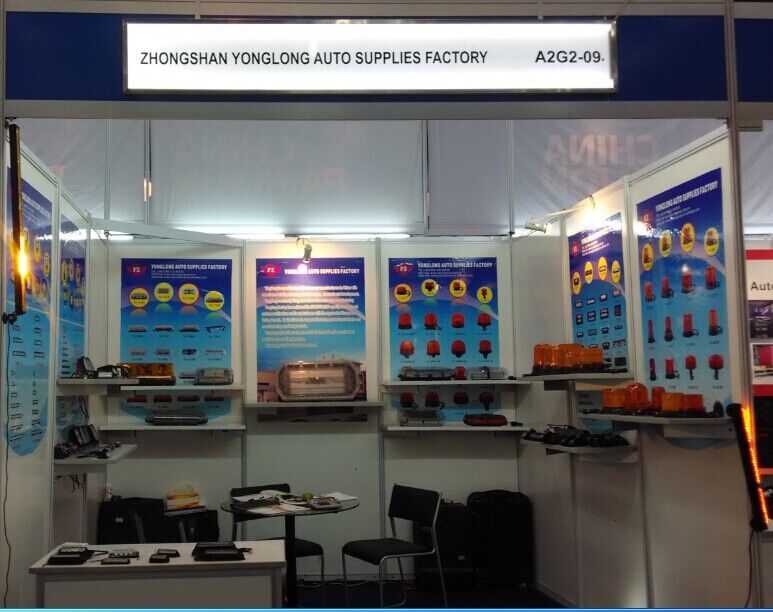
- 信息化的规划及实施严谨且有序可循:企业动力ERP上线时间6个月;PDM核心模块上线时间3个月,车间管理系统上线时间2个月。他们的规划一直本着严谨务实的作风,并对每个项目都有着严格的投入产出控制标准。
- 客户作为一家年轻的公司,具有追求创新,勇于突破的特点:求新目标强,历史负担少,人员阻力小,执行力强。
- 东信达坚持不懈的专业规划和稳定支持。在技术日益同质化的今天,一个好的供应商应该有这三个特点:供应商足够重视的态度;足够专业的解决方案;责任感强的服务团队。东信达实施团队始终坚持稳扎稳打,不急于求成,结合企业的现状进行规划并予以调整改善。
项目概况
此项目主要和ERP数据进行衔接,根据加工工艺要求,设置的现场工位管理和可视化结果输出,并将各种数据进行分析统计,以供管理人员循环改善。在不同工位上,依据工位的特点,根据加工工艺的不同,接收生产加工指令,将加工要求,图纸等注意事项传递给各工位加工人员,开工,完工、物品流转,实现快速人机交互及信息流转。并将信息回传至ERP系统,例如:操作员、开工时间、完工时间、异常情况、处理方法等,管理人员可通过ERP的看板报表进行及时反馈,跟踪检查并分析。
一方面提升生产工位的执行效率、工作准确性,使车间管理更精确到位;另一方面使得生产信息更加流畅高效,尤其是现场异常得到及时的反馈和解决。
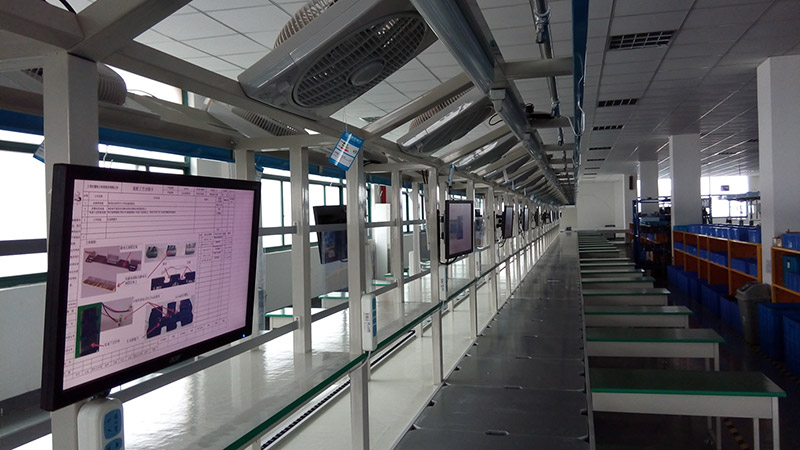
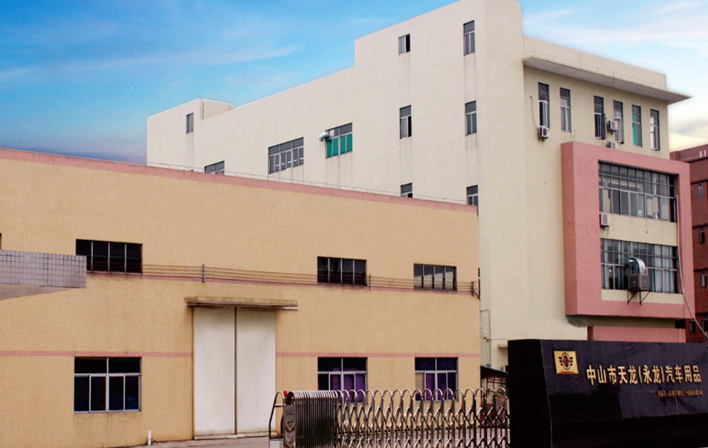
制造企业生产信息化系统规划与实施指南
制造企业该如何抓住企业问题的主要症结、产品生产特性来进行有效改良,从而提高生产效率,只要掌握方式方法,是充分可以实现的:
了解不同生产管理理念的差异,取长补短,抓住关键问题,循环改善
由于生产管理的复杂性,国内外关于生产管理的理论体系较多,大家较为熟悉的有JIT准时生产,精益生产制造、敏捷制造、柔性制造等理论体系。他们分别在不同的时期针对不同的企业有着良好的指导作用。
约束理论(TOC)是其中最有名的理论之一,它类似于木桶理论、短板理论。
它将任何系统都看成环环相扣的链条,链条的有效产出是由链条最薄弱的一环决定的。首先抓“重中之重”,使最重要的制约因素凸显出来,加以调整改善,然后持续分析,将当前最重大的制约关系抓出来,以此循环反复。
通过这种持续性的改善,既可抓大放小,又可避免疏漏,从而使得企业的整体管理水平持续提高。
分析问题从面到点,解决问题以点带面
企业问题的分析中应该遵循从面到线再到点的方式盘丝剥茧,在具体解决问题时以点带面的解决方式更有智慧。
通过对企业从主到次,从全盘到局部逐层寻找短板,企业可自主调研找到最关键的瓶颈流程:销售能力的高低,销售流程的顺畅、生产能力的不足,抑或是采购物料的缺位等。也可从以下几个方面着手:
- 原料,原料是否经常性短缺。如短缺,则增加生产过程的原料投入。
- 能力,即某种生产资源不足而导致市场需求无法满足,就要考虑增加资源。
- 市场,如果由于市场需求不足而导致市场能力过剩,就考虑开拓市场需求。
- 政策,找出企业内部和外部约束有效产出的各种政策规定。
而在具体某业务流程中,又通过对此流程的结果分析,找出其主要约束,例如通过企业的准时生产率,产品质量合格率等数据。譬如某企业的生产准时率较低,其主要约束有:
- 原材料短缺,不能齐套,导致无法正常开工。
- 主要生产资源:人员或设备能力不足。
- 主要工序:生产节拍不平衡,出现瓶颈工序。
- 变化因素多:急单,插单多,交货期频繁变更等
- 质量检测环节出现滞后等等。
在某个关键工序作业中,也需要通过对作业数据的分析,找出其主要约束并加以改善,从而实现从主到次,逐层发现主要问题并加以改善,方能真正解决问题。
优先在关键点上布局看板系统,快速见效,让团队充满信心
常言道,麻雀虽小,五脏俱全。企业再小,只要架构健全,总会有不同问题和瓶颈在不同流程,不同部门存在着。因此依据自身现状,找到关键的业务节点,并设置可视化看板系统,以结果带动过程,是较有效的方法。
可视化看板系统不仅可布置在企业内部,云端、客户方、供应商方等,了解看板的不同作用进行分类,可让思路更加清晰:
调度看板
生产管理人员可依据订单的变化,生产的状况进行当期生产调度及调整。调度人员可查看订单的物料库存状况,设备的产能情况,以及当前生产进度等。
工位看板
主要作用于生产工位,可用于工序流转,数据采集,作业指引,设置预警等,也可设置工位加工的视频输出给到重点客户查看。
管理看板
为管理者或客户输出的生产状况看板,依据不同用户的需求和管理目标,从而达到预警、监控、预防、管理、结果输出的作用。
协同看板
此处主要指外部系统,客户或供应商,其目的是抓住协同节点,高效预警、交互,从而达到快速准确的配合目标。
预警看板
预警看板精准定位到人,可将那些环节可能存在或已经发生的问题及时反馈给相关人员及其主管。
企业需要严谨务实态度,切勿贪多求全、眼高手低,应根据自身情况做好规划。
目前市面上有各种各样的理论数据工具,良莠不齐,让人眼花缭乱。因此企业需要保持冷静,客观灵活加以规划,从而建立自己的主心骨。
知己知彼
企业管理者需要对自己的企业有清醒的认识,还需要有一定的理论知识,同时实时了解最新的技术工具。
抓大放小
面对问题,不少人员会出现急躁、迷茫、怀疑、犹豫等情绪,干扰了判断。只有沉下心来找出最根本的痛点,才能从主到次加以循环改善,逐一解决问题。
明确导向
不少企业只是将各部门的问题简单汇总,导致各自为政,缺少主体规划,缺失明确导向,多头目标,是不少企业失败的主要原因。
制订校验指标
客观的数据校验标准,设定业务改善指标,财务指标,分清长期、中期及短期利益,让人更加清醒,少走弯路。